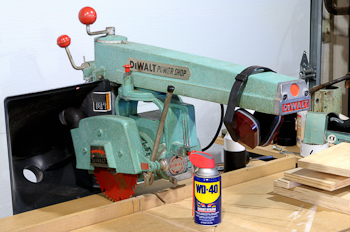
This is a radial arm saw with all the parts assembled. WD40 can for scale in all images.
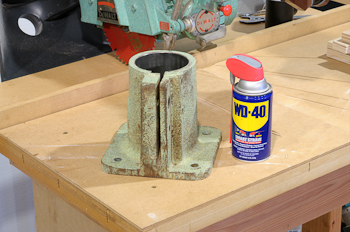
The column base (Cast Iron, has machined interior surface and threaded holes)
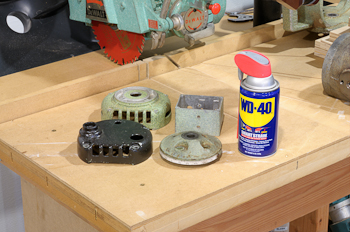
The two motor end bells (aluminum with machined surfaces for the bearings), thrust cap (cast iron) and electrical box for motor (aluminum)
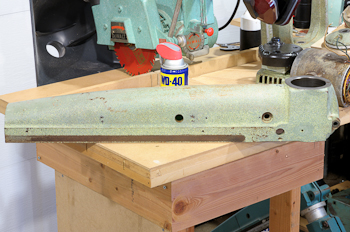
The arm (cast iron). It has machined surfaces where it rests against the column and threaded holes.
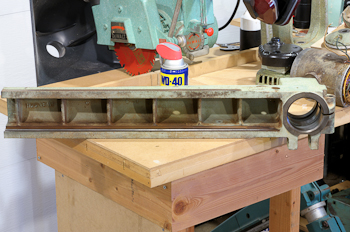
The arm on its side showing the machined "ways" where the roller carriage travels.
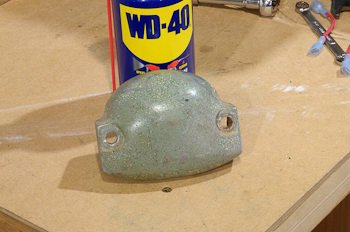
This is the "nose" cap that goes on the end of the arm. It's thick aluminum.
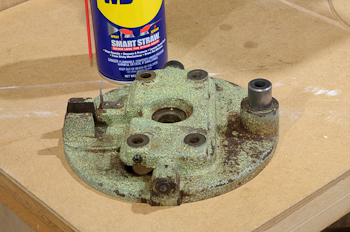
The roller carriage (cast iron) top view - it has threaded holes for set screws

The roller carriage (cast iron) bottom view showing machined surfaces.
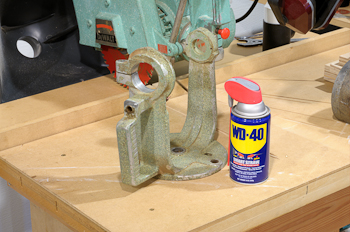
The yoke which holds the motor (Aluminum). It has threaded holes for set screws and a brass lined hole for the indexing pin.
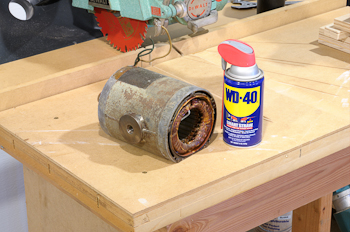
The motor housing (can't be powder coated as the insulation would melt in the oven)
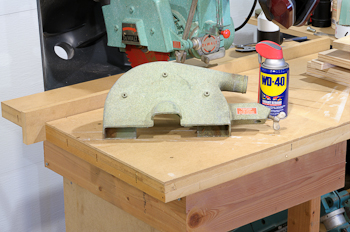
The blade guard (Aluminum). It has a large threaded hole.